フレットをファンフレット化したTP001は試作品のためヘッドのインレイを施していませんでしたが、せっかくなので今回はインレイでロゴマークを付けようと思います。
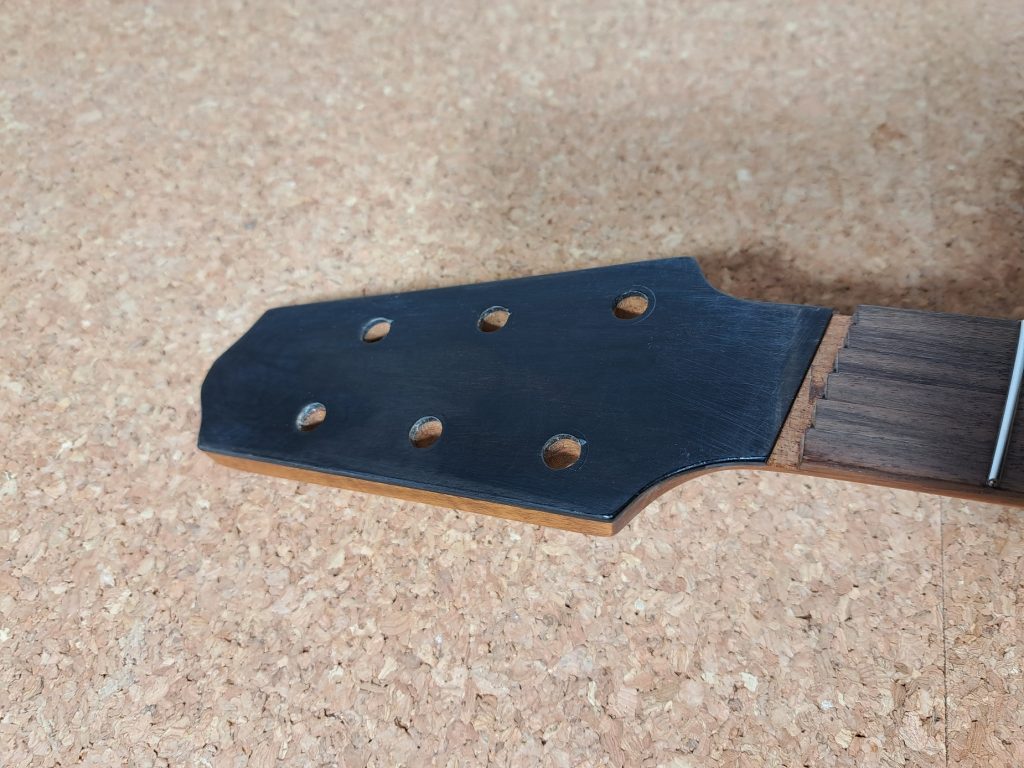
インレイ材料の作り方としては白蝶貝やアバロンの板材に型紙を貼り付けて型紙のパターンの外側を糸ノコを使って少し大きめに切り出してからヤスリで整形してしていました。昔ながらのやり方でやっていたのでですが細かくて大変です。
近年、レーザー加工機が安価に入手できるようになり、昨年自分も導入しました。私が導入したのは30WのCO2レーザーカッターbeamoです。
ネットで調べてもインレイ用途でCO2レーザーを使用している情報が少ないので、今回試してみることにしました。
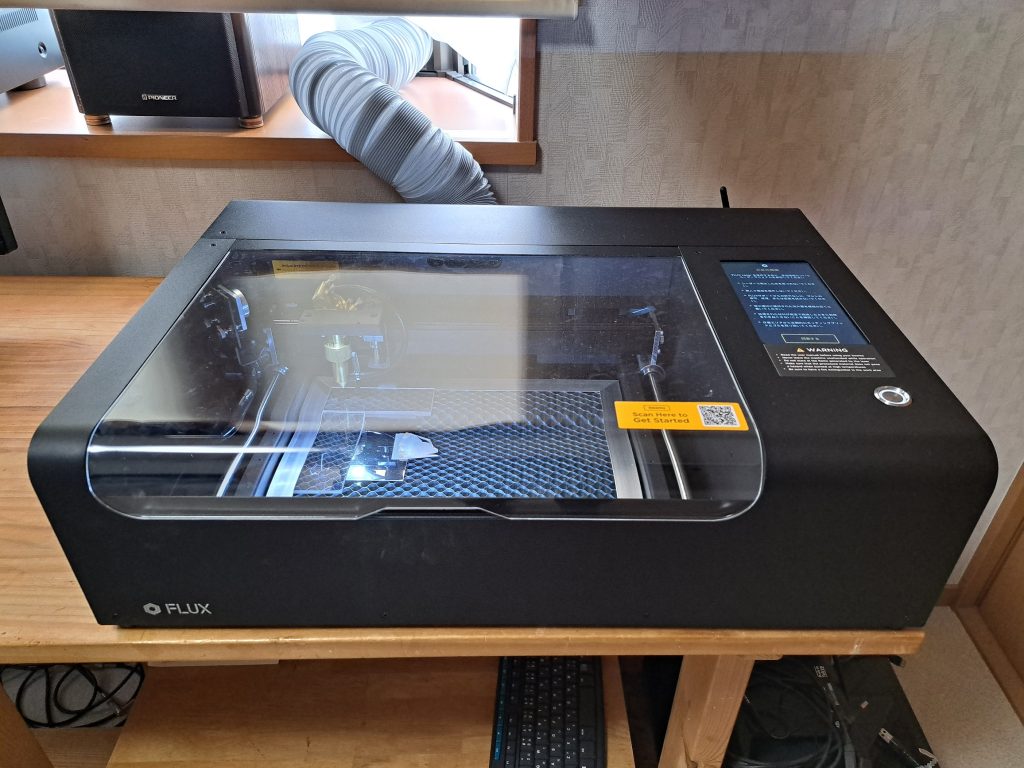
最初、厚さ1.5mmの白蝶貝をbeamoで切れるか試した時は表面が白くなるだけで全く切ることはできませんでした。その後色々試して今は何とか使えそうなことが分かりうれしく思っているところです。
現在の方法を紹介したいと思います。
まず、四角のSUS板に材料の貝殻を両面テープで固定し、それを装置内部にセットします。
SUS板は取り外し後再度セットした時に位置が再現するようにしています。
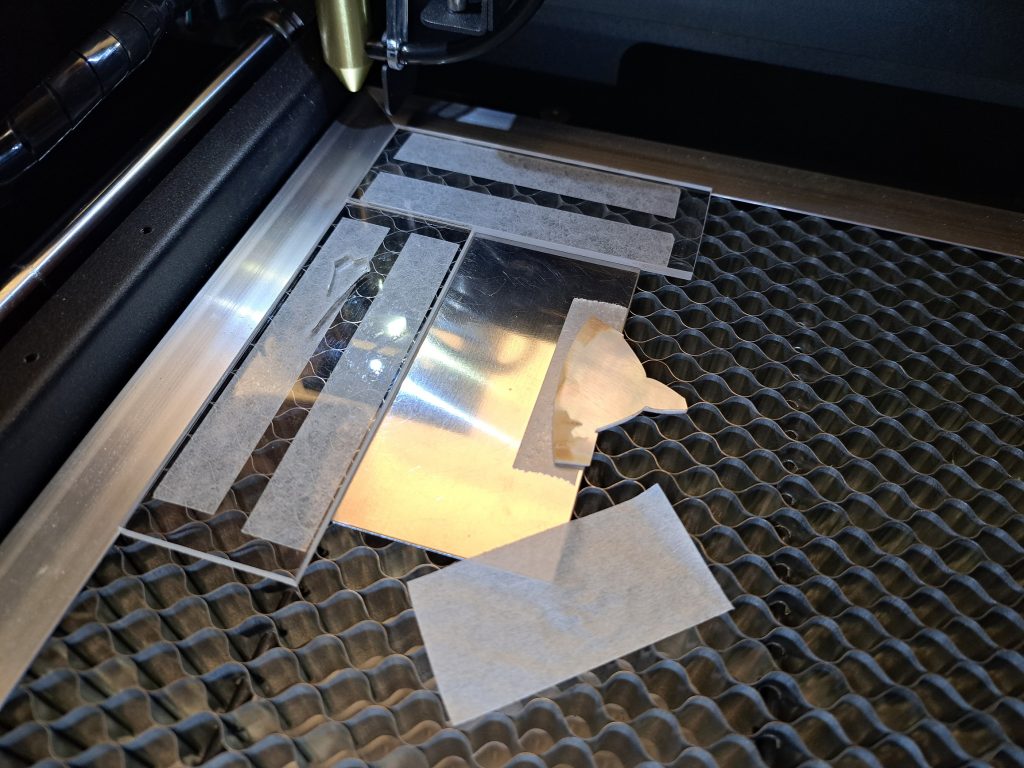
下はbeamoの画面になります。今回はロゴマークの一部を切り出します。
レーザーヘッドにカメラが付いていて材料に対してカットする位置を画像を見ながら合わせられるのが便利です。
カットする条件は出力55%、速度20mm/s、実行回数3回でやっています。
速度を遅くすると熱の影響が出てしまい、インレイ自体がもろくなるので、瞬間加熱的な方が良さそうです。
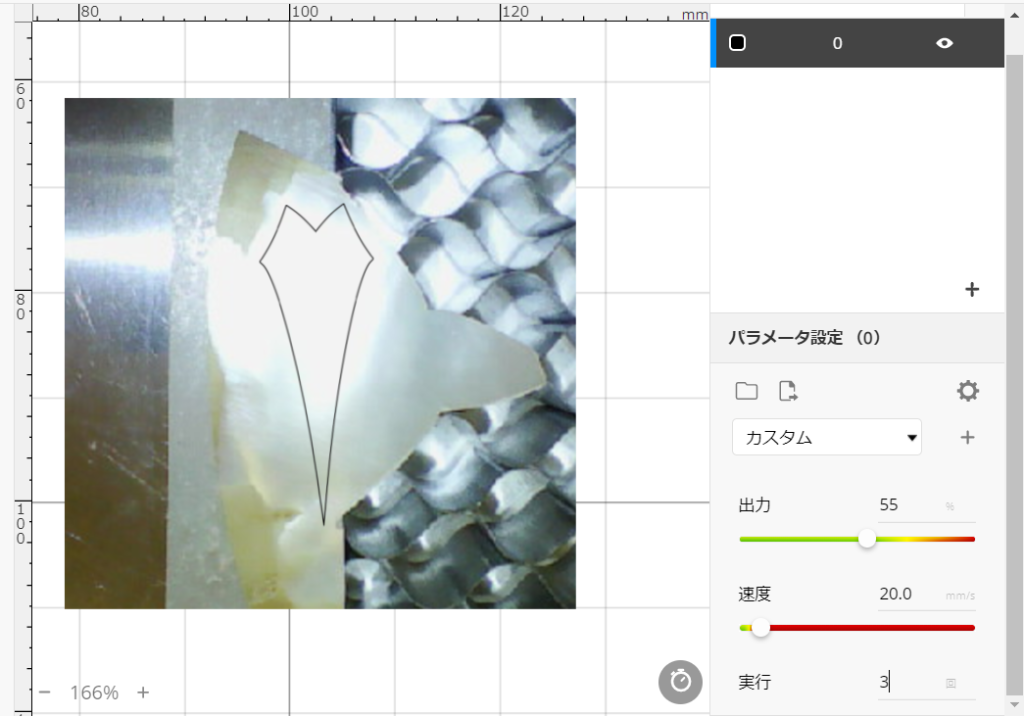
下の写真は1回目の照射後です。
写真の様にレーザー照射したところが白くなりますが切断はできません。しかし、白くなったところはカッターの刃で削れるようになります。粉となって削り取ることができます。ほじれるところまでほじると約0.3mmの溝になります。
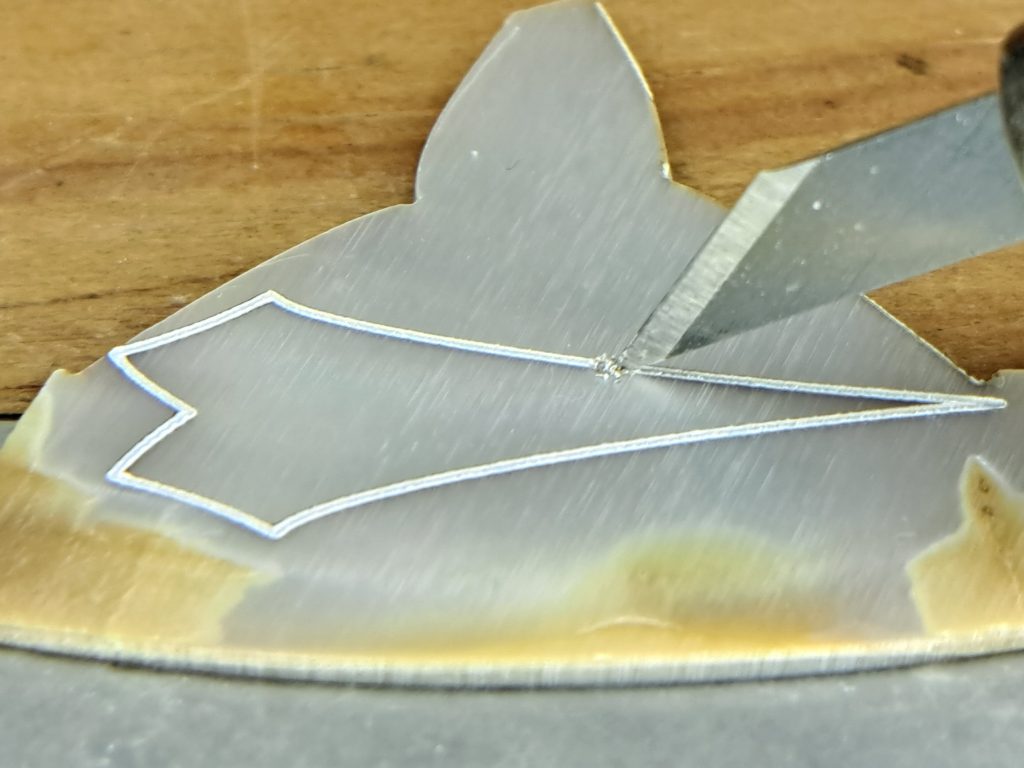
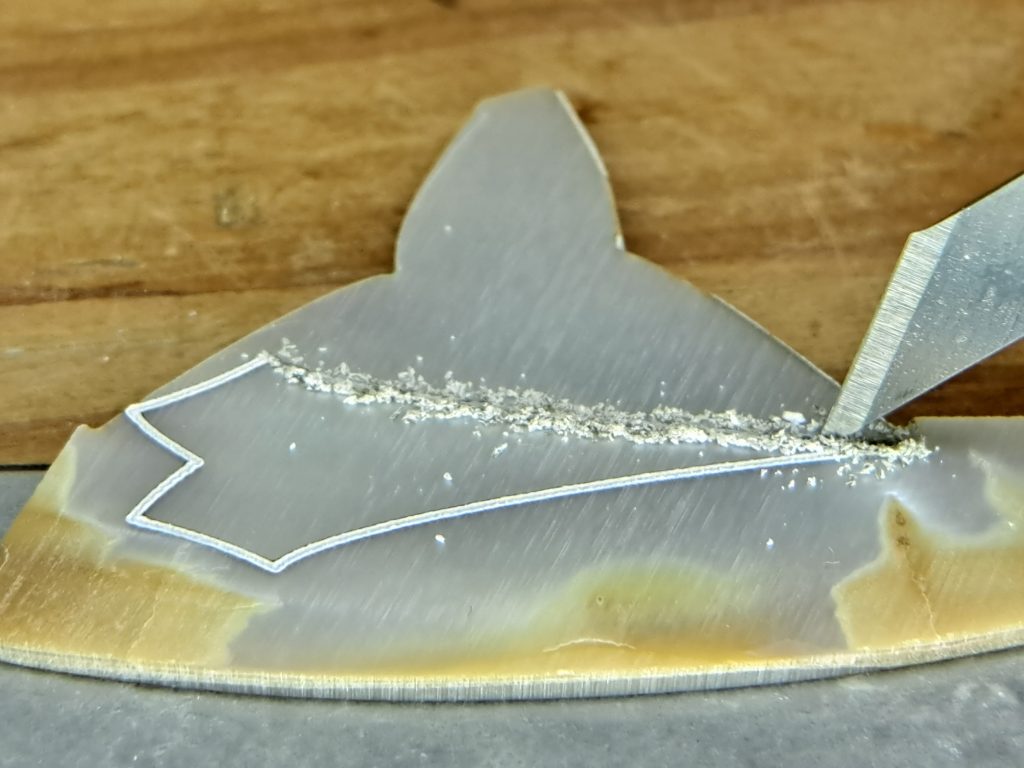
照射しては削りを繰り返します。照射時はレーザー光の焦点を削った溝の底に合わせると有効なことが分かったため、削った溝の深さに合わせて0.5mm間隔でSUS板の下にスペーサを追加していきます。
以下は4回目から6回目の照射削り後の写真です。溝が深くなるほど光が入らなくなるため削れる量が少なくなっていきます。溝の幅は約0.4mmです。
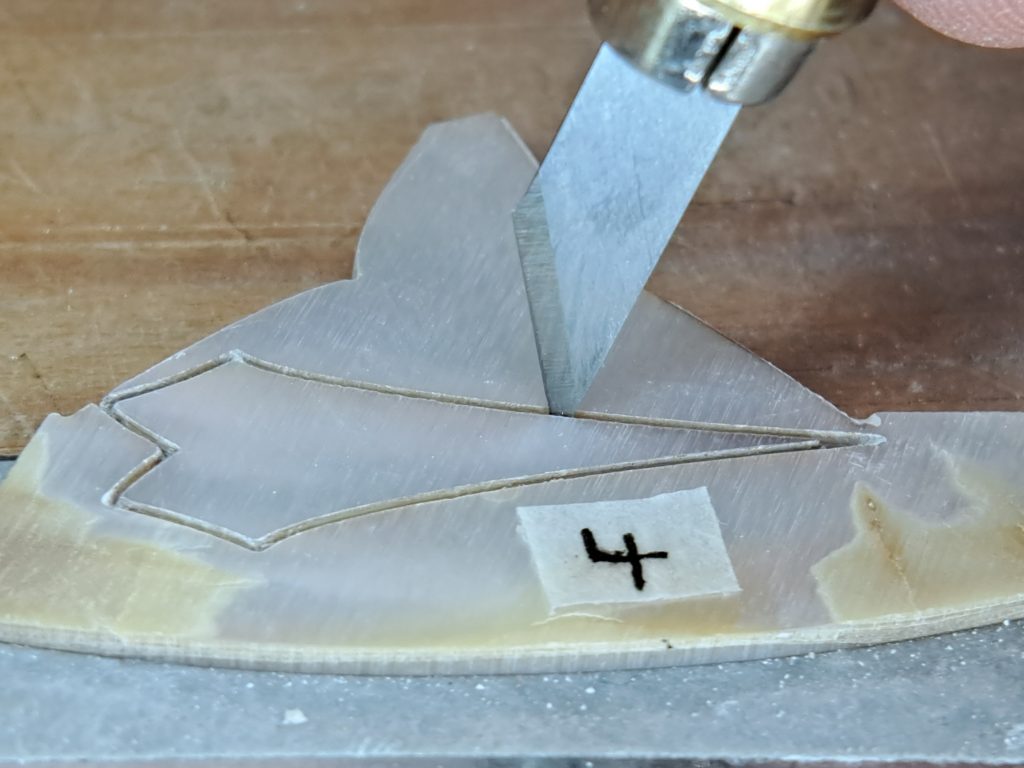
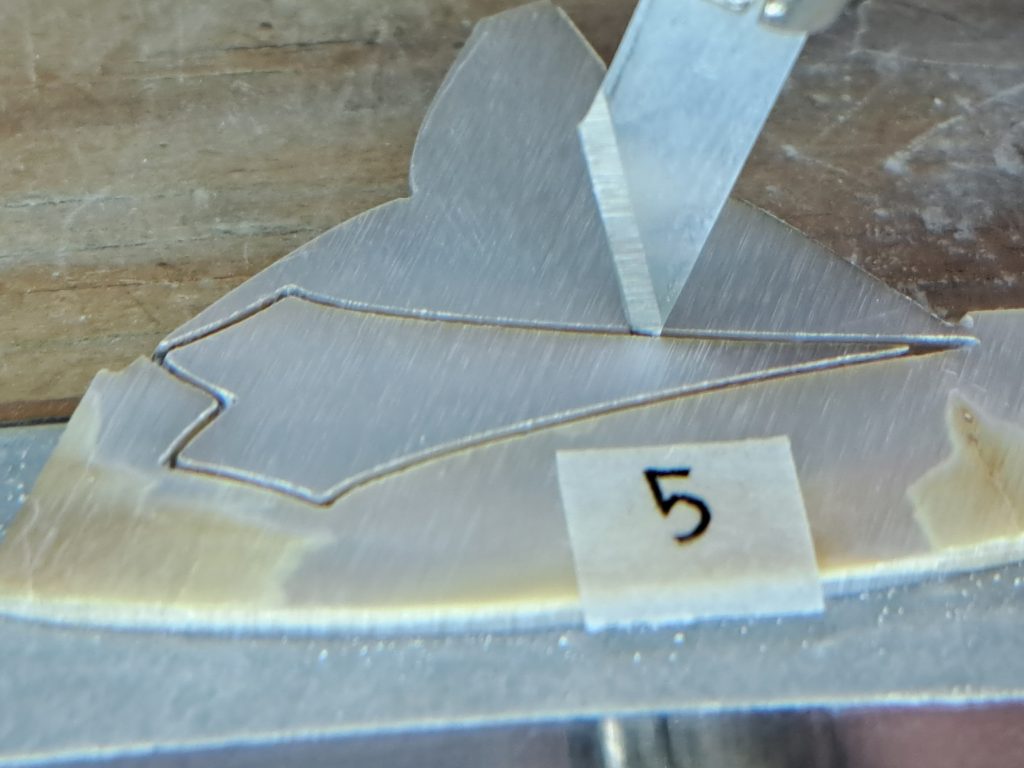
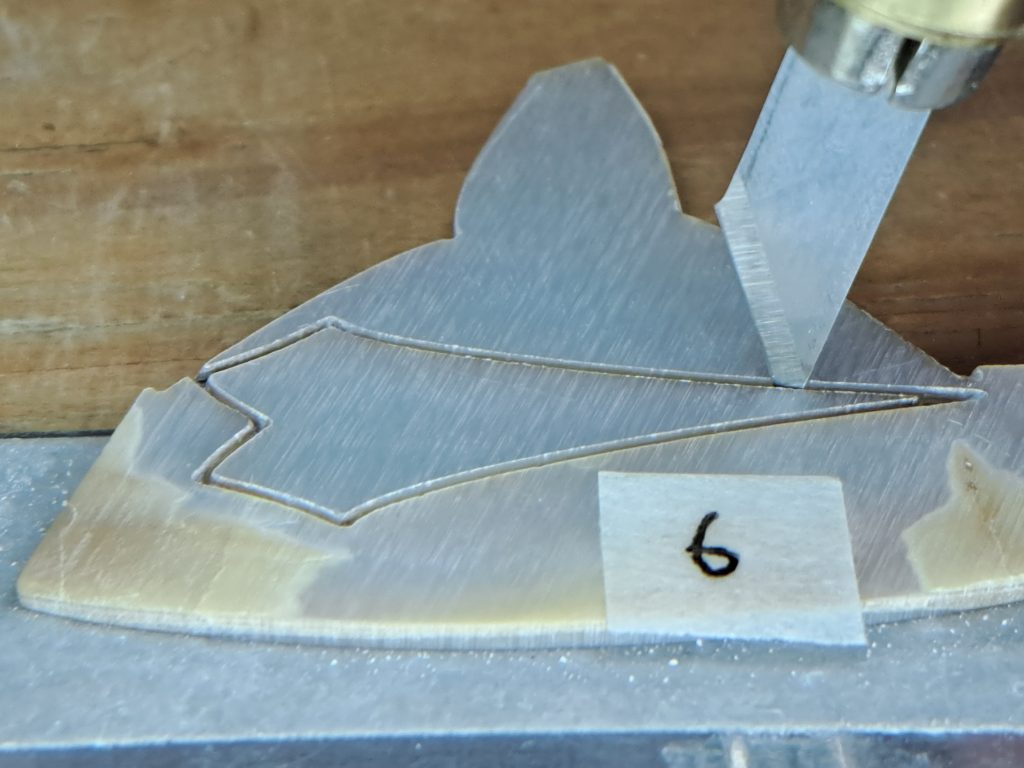
7回目でようやく切断できました。
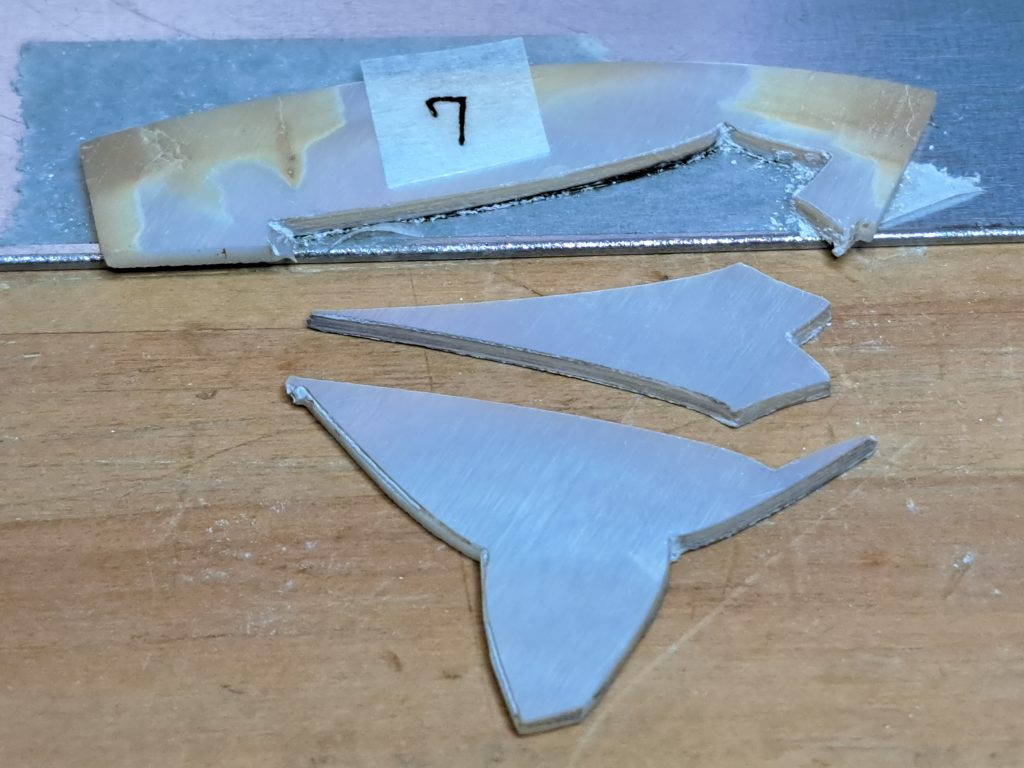
レーザーを当ててカッターでホジホジしただけでこのレベルに仕上がり、アバウトな糸ノコを使わなくて済むのので、照射回数はちょっと多いですがメリットはあるかと思いました。
最後に切り出したインレイを並べてみました。
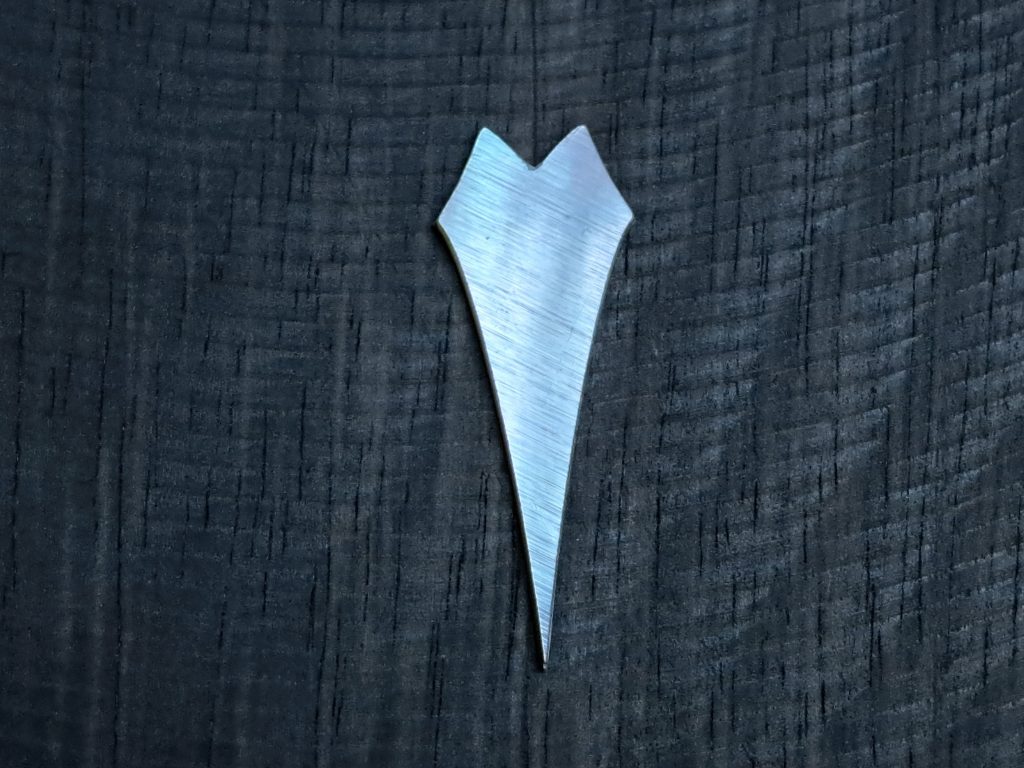
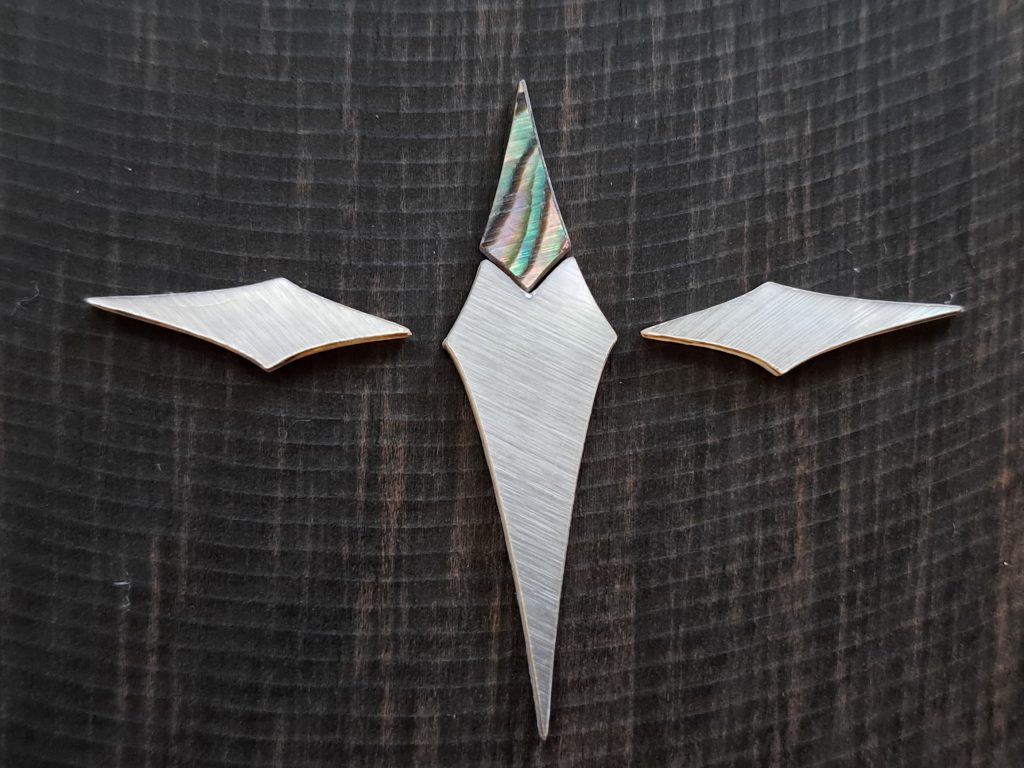